La selle en polyester
Nous sommes en Janvier 2008 et je viens de recevoir la selle commandée chez Facs Moto. J'ai choisi d'acheter la selle (plutôt que la construire) essentiellement pour gagner du temps.
La qualité est excellente (aussi bien l'épaisseur de la fibre que la finition), pour un prix correct et un délai d'expédition rapide. Bref, que du bon, vous pouvez commander en toute confiance
!!
Bon, je vais quand même y mettre une petite touche personnelle ...
En fait, je compte intégrer le feu arrière dans la selle et ajouter un dessous de selle avec le support de plaque et son éclairage.
Préambule sur l'utilisation des produits qui suivent
Les pièces réalisées sur cette page nécessitent l'emploi et la manipulation de produits classés dangereux. Il est absolument
indispensable de respecter les consignes de sécurité marqués sur ces produits.
Pour ma part, je travaille toujours dans un local aéré (même en hiver) et je porte systématiquement un masque, des lunettes, des gants (même s'ils sont roses

) et des vêtements appropriés. Si malgré ces précautions, on se retrouve
avec un peu de résine sur les doigts, ça s'enlève très bien à l'eau chaude + savon + brosse à ongle, mais n'utilisez
jamais de solvants en guise de liquide de rinçage comme on peut le voir sur certains sites !
La fixation de la selle au cadre
Tout d'abord, je ne veux pas de vis de fixation apparentes sur l'extérieur de la selle. Je veux aussi que tout l'ensemble soit monté sur silentbloc (ben ouai, je tiens à mon confort

).
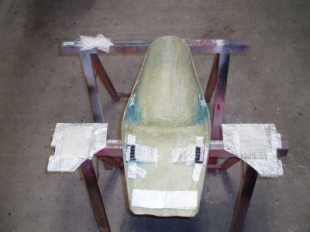
Je vais réutiliser les 2 appuis rectangulaires en caoutchouc d'origine. J'enduis une face de résine et je positionne la selle. C'est provisoire, ils seront renforcés à la fibre de verre en final.
De même, j'utilise les 2 trous de fixation de l'avant de la selle et j'y adapte 2 butées en caoutchouc (ce qui fait 4 butées en périphérie pour l'instant).
Une butée centrale réglable en caoutchouc est ajoutée sur l'arrière et au centre de l'assise, et ça devrait être bon avec tout ça (ça fait 5 appuis caoutchouc au total).
Pour le maintien arrière de la selle, 2 pattes sont réalisées dans une tôle inox est fixées à la résine (en attendant le renfort de fibre de verre). La liaison au cadre de ces 2 pattes est aussi sur silentbloc.
Les fixations de la selle terminées (après renforcement version "costaud", et en plus ça se monte pile-poil) :
Le moulage du dessous de selle
Comme évoqué au dessus, je compte réaliser un dessous de selle en fibre de verre qui intégrera le feu arrière, le support de plaque, le passage du pneu et qui sera lié à la selle initiale.
En résumé, ça fera un caisson sur l'arrière de la selle (je sais, c'est pas simple à comprendre comme ça, mais tout va être limpide avec les photos qui suivent

).
Le feu arrière :
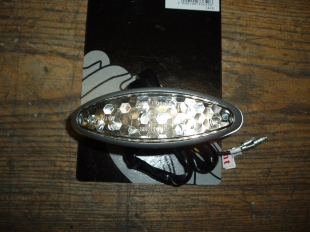
J'ai beaucoup hésité pour choisir le feu : un petit rond pour un look rétro ou un récent à leds ?
C'est au final un feu à led qui est retenu (pour changer un peu de ce qui se fait habituellement sur les Cafe Racer, et aussi parce que les leds résistent mieux aux "good vibrations"

).
Comme je n'ai rien trouvé chez les accessoiristes français, le feu a été acheté dans le catalogue Louis.de (en Allemagne).
Le moule perdu :
Comme la forme va être un peu compliquée, je choisis de faire un moule perdu (direct en négatif) pour le dessous de selle en utilisant des plaques de polystyrène expansé (ça se travaille très bien).
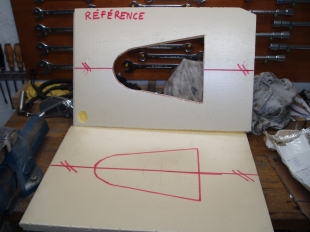
La première étape est de partir de la forme
intérieure de la selle. Elles est simplement tracée à partir de la selle sur une plaque de polystyrène expansé.
La forme intérieure est ensuite découpée, puis la plaque sera collée sur la seconde.
A ce stade, la partie basse du caisson est presque prête. Avant le collage, il reste quand même à y inclure le support de feu arrière, le support de plaque et une forme pour le passage du pneu.
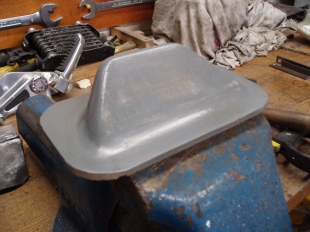
Pour le support de plaque, c'est un peu compliqué car le négatif est en forme intérieure (pas facile à tailler).
Je vais donc réaliser la forme finale (en positif), puis tirer un négatif de cette forme qui sera fixé sur la plaque de polystyrène.
Le modèle final est réalisé avec des plaques de contreplaqué bois et du plâtre, puis le tout est taillé, poncé, enduit, re-poncé ... jusqu'à temps que ce soit bon.
Il est ensuite apprêté, puis très bien ciré (5 applications/lustrage).
3 couches de mat de verre (300 g/m²) + résine polyester sont appliquées sur le support précédent.
Le démoulage se fait sans problème.
Après nettoyage, ce négatif va être intégré au moule complet.
Pour le passage du pneu, j'utilise un morceau de tube PVC (diamètre 100) que je découpe. La forme du support du feu arrière est directement taillée dans le polystyrène.
Une fois toutes les formes intégrées, le moule est apprêté (avec une peinture à l'eau), puis très bien ciré (toujours 5 applications/lustrage).
Le moule perdu terminé :
Il reste quelques petits défauts, mais je les supprimerai sur le moulage définitif.
On a vu que l'avantage du polystyrène expansé est qu'il se travaille très bien.
Son inconvénient majeur est qu'il fond littéralement en présence de certains solvants (notamment ceux contenus dans la résine polyester, dans les mastics et les apprêts à base cellulosique). C'est pour cette raison que la couche d'apprêt était une base à l'eau.
Une des meilleures solutions pour mouler sur du polystyrène est d'utiliser une résine époxy (bon, il existe aussi des résines polyester spéciales sans solvant (le styrène), mais qui dit spéciales dit distribution limitée, donc généralement des produits chers ...).
Tous les produits que j'utilise ici sont des classiques qui se trouvent dans toutes les grandes surfaces de bricolage.
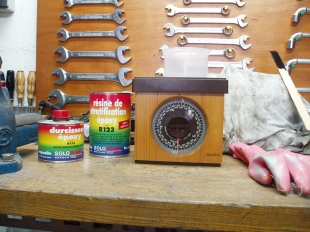
Pour ma part, je trouve que les avantages de la résine époxy sont qu'elle ne fait pas fondre le polystyrène (ça, on vient de le voir),
qu'elle n'absorbe pas l'eau (dans le cas du dessous de selle, on s'en fout un peu), qu'elle résiste mieux à l'essence actuelle que la résine polyester
(on s'en fout aussi), et enfin que ses caractéristiques mécaniques sont supérieures à celles de la résine polyester (çà on s'en fout pas

).
Pour les inconvénients, elle est un peu plus chère, la mise en œuvre est plus contraignante, le temps de séchage est plus long (au moins 24 heures), et surtout je trouve que l'imprégnation du mat de verre est beaucoup plus difficile.
Quelques conseils pour la mise en œuvre :
- Bien mélanger chaque produit (la résine époxy et le durcisseur) avant de commencer le dosage,
- Doser précisément les produits (j'utilise une balance de cuisine précise),
- Bien mélanger les produits,
- Travailler à une température comprise entre 15 et 20°C,
- Laisser polymériser au moins 48 heures à cette fourchette de températures,
Après avoir appliquées 3 couches de mat de verre (300 g/m²) en sandwich avec 2 couches de rowing (tressé 290 g/m²), le tout lié avec la résine époxy, le moule est ouvert (plutôt cassé à cause des contre-dépouilles).
Les petites défauts (essentiellement des bulles d'air) sont corrigés au mastic renforcé à la fibre de verre (appelé "choucroute"). Les bords du moulage sont tronçonnés et poncés. Les trous de fixation du phare sont percés et le tout est grossièrement poncé.
Voilà ce que donne le résultat du moulage du dessous de selle : ce n'est esthétiquement pas terrible, mais c'est normal.
L'intégration du dessous de selle à la selle
Cette étape consiste à lier de manière définitive le dessous de selle au dessus de selle. Il faut tout de même noter que les 2 matériaux sont différents : la selle est en résine polyester armé de fibres de verre et
le dessous de selle est en résine époxy armée de fibres de verre.
Il n'y a pas d'incompatibilité entre ces 2 matériaux, mais le comportement aux contraintes mécaniques importantes sera différent et pourra occasionner des fissurations ou des micro-décollements.
Il est conseillé dans ce cas d'utiliser de la résine époxy comme liant, après avoir pris soin de bien poncer et nettoyer les surfaces de liaison de chaque pièce à assembler.
Bon, ça c'est la théorie, après ce n'est qu'un dessous de selle ... des contraintes mécaniques importantes, il n'y en aura pas beaucoup

.
Je vais quand même utiliser de la résine époxy (en fait, surtout parceque je n'ai consommé que la moitié de la quantité achetée et que le reste va être perdu si je ne l'utilise pas).

Déjà, avant d'attaquer la liaison définitive, les 2 pièces sont positionnées et fixées l'une à l'autre avec quelques points de "choucroute" (du mastic renforcé à la fibre de verre pour ceux qui ne suivent pas).
J'ai fait le choix de cette étape pour pouvoir vérifier la géométrie de l'ensemble assemblé et surtout garantir l'absence de mouvements d'une pièce par rapport à l'autre pendant les 48 heures de polymérisation.
La selle est donc fixée au cadre, et le dessous de selle est calé pour que tout soit au poil, et 4 points de "choucroute" sont posés.
Après quelques heures, l'ensemble est démonté avec précautions (ce n'est pas très solide à cette étape) et est mis au soleil de printemps (pour une fois qu'il est là dans la Marne, j'en profite

) pour terminer la polymérisation.
La résine époxy armée de 5 couches de fibres de verre est posée pour lier définitivement les 2 pièces. Comme la selle est démontée du cadre, c'est bien accessible.
Après 48 heures de polymérisation, les raccords entre les 2 pièces sont terminés à la "choucroute", puis poncés / mastiqués / poncés ... jusqu'à ce que ce soit parfait.
Les 2 pièces assemblées :
Nota : 2 inserts métalliques ont été intégrés dans le dessous de selle pour pouvoir fixer la plaque d'immatriculation. Je n'ai trouvé que cette solution, car il n'y a pas d'accessibilité
pour pouvoir poser des rivets (le support de feu arrière gêne).
Après un dernier ponçage au grain 600 (à l'eau), l'ensemble reçoit une couche d'apprêt.
Comme je voudrais vraiment voir ce que ça donne, la selle va être montée sur le cadre avec les accessoires.
D'abord, il faut fixer le feu arrière et ce n'est vraiment pas accessible pour mettre en place les écrous de fixation (il faut des mains d'enfants),
et surtout il n'est pas possible de les serrer avec une clé (elle ne passe pas).
Pour arranger ça, 2 écrous longs en laiton sont réalisés.
Pour les visser, un tournevis flexible est utilisé (le 6 pans des écrous correspond au 6 pans creux du tournevis ... une côte à la noix bien sûr

).
Une fois le phare fixé, j'imprime vite fait une plaque d'immatriculation (sur papier) pour voir ce que ça donne.
Après quelques essais, le bon format de la plaque (esthétiquement parlant

) est trouvé (
et bien sûr, les dimensions ne correspondent pas à celles homologuées).
La selle montée vue de l'arrière : je trouve la photo bizarre (ça fait photo truquée), mais je n'ai uniquement retouché que les numéros de la plaque.
La selle montée vue de l'arrière (sous un autre angle et sans la plaque) :
Une dernière vue de côté :
Bon, je vais pouvoir tronçonner l'arrière du cadre maintenant (là où il y a du scotch).
L'assise de la selle
Toujours pour avoir une selle confortable, je choisi d'avoir une assise complètement démontable de la selle et qui sera recouverte d'un skaï.
La première étape est de mouler le support de l'assise directement sur la selle. Le périmètre est délimité au moyen de pâte à modeler (merci Léa

), puis la selle est cirée/lustrée 5 fois de suite.
Ensuite, 4 couches de mat de verre (300 g/m²) liées avec de la résine polyester sont appliquées pour constituer la première partie de l'assise.
Après polymérisation, ce premier moulage est décollé (si on a bien ciré, ça vient tout seul), et les bords sont grossièrement découpés (la finition sera pour plus tard).
Pour la seconde étape, ce moulage est reposé sur la selle et fixé au moyen de 5 vis (qui seront prises en sandwich entre les 2 parties de l'assise). A ce stade, il faut vérifier où l'on perce : comme l'assise se monte en dernier,
il est impératif que les écrous soient accessibles pour monter/démonter l'assise.
La dernière étape est de recouvrir ces vis de 3 couches de mat de verre (300 g/m²) + résine polyester.
Après polymérisation, les bords sont précisément découpés pour s'ajuster à la forme initiale de la selle.
Le support de l'assise de la selle terminé :
Le support de l'assise en place :
Il ne reste plus qu'à coller une mousse et recouvrir le tout d'un skaï.
Comme je n'ai pas les matériaux (ni mousse, ni skaï), j'ai fait faire cette partie en Juillet par "La Sellerie Champenoise" : excellent boulot pour un prix raisonnable

.
Conclusion de cette page
Cette page est maintenant terminée. Comme depuis le début, la selle a été beaucoup plus longue à réaliser que prévu ... bon, j'ai aussi passé moins de temps
que je ne l'aurai voulu (en fait, je n'aime pas travailler au froid le soir dans mon atelier

).
Le travail du polyester (ou l'époxy) est :
- long (il faut bien respecter les temps de polymérisation)
- pénible (des lunettes, un masque, des gants ... la résine colle partout, il y a des fibres de mat partout, quand on ponce ça fait de la poussière très volatile et irritante)
Mais aussi
- assez bon marché (les produits se trouvent dans toutes les grandes surfaces de bricolage)
- pas très compliqué à réaliser
Donc, si vous êtes tentés, lancez-vous ! En prenant votre temps et en étant tenace (il ne faut pas se décourager et il faut persévérer), vous sortirez des pièces vraiment sympas et originales, et perso
j'adore le coté "
c'est moi qui l'ai fait !"